Wicks Forge is Moving!
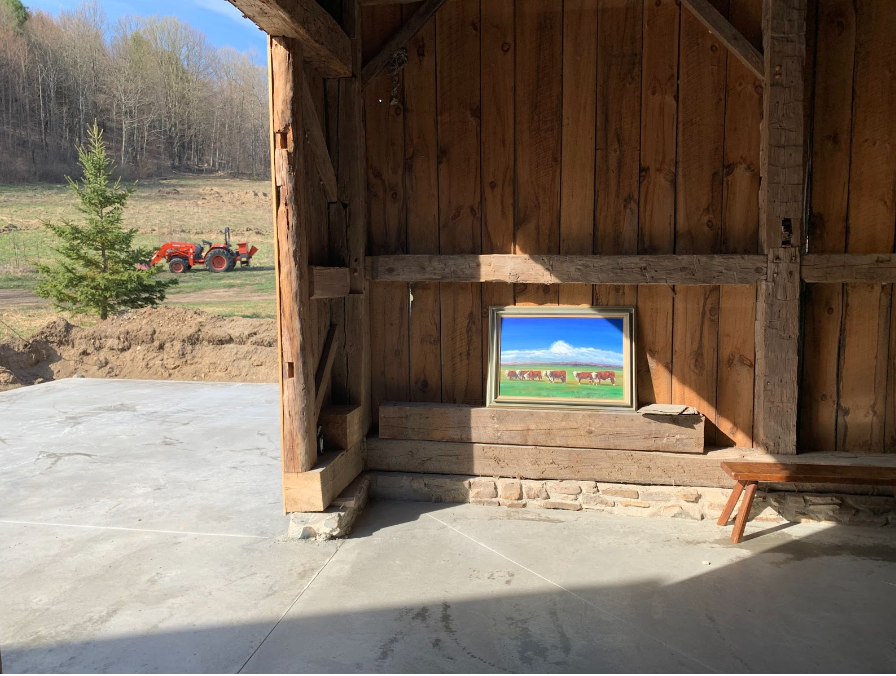
We've got some big news.
We're moving!
Many of you have become familiar with the Wicks Forge shop through the photos and videos we’ve shared on our Instagram and Tiktok. We’ve been there for a few years now and the space has become a second home for our team, but we’ve outgrown the old barn and it’s time to move on to bigger and better things!
The reason we’re sharing this with you, is that we’re going to be going through a bit of a transition period. You’ll still be able to shop on our website, but we’re asking for your patience with us as we make the big move and work to get set up in the new space. During this time, we may be out of stock of a few things and won’t be able to offer personalizations for the time being. But don’t worry, we’ll still run a Father’s Day sale (stay tuned!), so dad can get the awesome hand forged gift he deserves.
Workspaces change, Wicks Forge is forever bootleg
In honor of our new space and in the spirit of nostalgia, we thought it'd be cool to share a look back at some of the workshops we've had over the years. We're super excited for this next phase of Wicks Forge and look forward to sharing lots of updates over the coming year as we build out the new shop.
The Chicken Shed
Whether it's using repurposed spaces or homemade tools, there's always been a big DIY ethos to Wicks Forge. This started all the way back when I was apprenticing with Jim Whitson in Scotland.
I got to work on some of the most amazing architectural ironwork being created today. But Jim's shop was a chicken shed. That's not some Scottish slang. The place was literally a big long shed for raising chickens that he re-purposed into a workshop. It was in a hamlet in the countryside outside Edinburgh surrounded by sheep farms. It was so remote, I got lost my first time taking the bus out there and had to get directions from a fellow whose Scottish accent was so strong I couldn't be certain we were speaking the same language. The shop had low ceilings and cracked floors and all manner of gnarly old tools. But it was also a paradise of creation. I learned that the space means little compared to one's ability to create with that space.
Grandpa's garage
When I got back to the US, Wicks Forge was officially born in my grandparent's garage. While helping them transition into assisted living, I began unearthing all of my Grandfather's family metalworking tools that he had held onto since closing his own metalworking business (Wicks Products) in the 1980s. Some of the tools went all the way back to my Great Great Grandfather, who had worked as a metal polisher on the Statue of Liberty.
I used these family tools and a homemade forge to get Wicks Forge off the ground. I had a minimal set-up of equipment and a giant old Buick Lesabre parked in the garage. I had to drive out of the way anytime I wanted to work on projects. Between weekly noise complaints from neighbours and an unused college diploma, I definitely questioned my life choices regularly.
The Pottery Barn
After my grandparents moved into assisted living, their house was sold and I lost that workshop space. A friend let me set up a few tools at his barn pottery studio.
At that time, I had another full-time job in a different state several hours away and I was only able to work on orders each weekend. I would drive two hours to Connecticut every Friday after work and crash in a friend's basement.
Saturdays and Sundays I would head to the barn, set up my little makeshift shop in the corner of the studio and work on orders, before driving back Sunday nights to start my other work week.
The Horse Shed
A few years later, I moved Wicks Forge to Maine. The business had grown over the years but my tool collection grew even faster. My friend and I rented a 30-foot box truck and did a 36-hour whirlwind round-trip drive to pack up and relocate the shop.
The new space was in part of an old barn on a horse farm. There was no insulation, one small heater, no electricity, and dirt floors. My first winter there it got down to -20. It was so cold that the propane tank I used for my forge froze and I had to set up my only heater– not to keep me from hypothermia, but to keep the propane tank thawed. But we made that workshop into a powerhouse production center in the usual DIY Wicks Forge way (see our blog post on the Goblin Workshop for more details).
It’s there that I learned how to swing a hammer while wearing 5 sweatshirts in February, and it’s also where our team started to grow from just myself to now a whole ragtag group of artists and ne'er-do-wells.
This is the shop we’re saying goodbye to now.
The Milk Barn
All of these spaces over the years were great but none were really a permanent space. We had to run electricity lines attached to drier outlets and set up tumbling machines in horse stalls. It was a fun adventure but we couldn't really transform the spaces for the exact type of creation we wanted to do.
Last fall things changed and I had the opportunity to purchase an old farm with a college friend of mine who is an organic farmer.
The farm used to host a dairy operation, but has been out of commission for a generation or more and is in need of lots of TLC. But, there was a big old barn on the property just waiting to be brought back to life. And for the first time, since I started Wicks Forge, we now had a permanent space to continue growing and finally call our own.
The team and I have spent the last 6 months slowly getting the new space set up, putting in floors, and preparing to add a 2,000 square foot addition. We're so excited for this next phase and what it will mean for the new creations we'll be able to get out to folks in the years and decades to come.

Hopefully you will be settled and up and running in your new location by early September! My sister from Illinois will be visiting me in Maine and we want to stop in!!!
What town are you moving to?