The "Goblin Workshop" 2
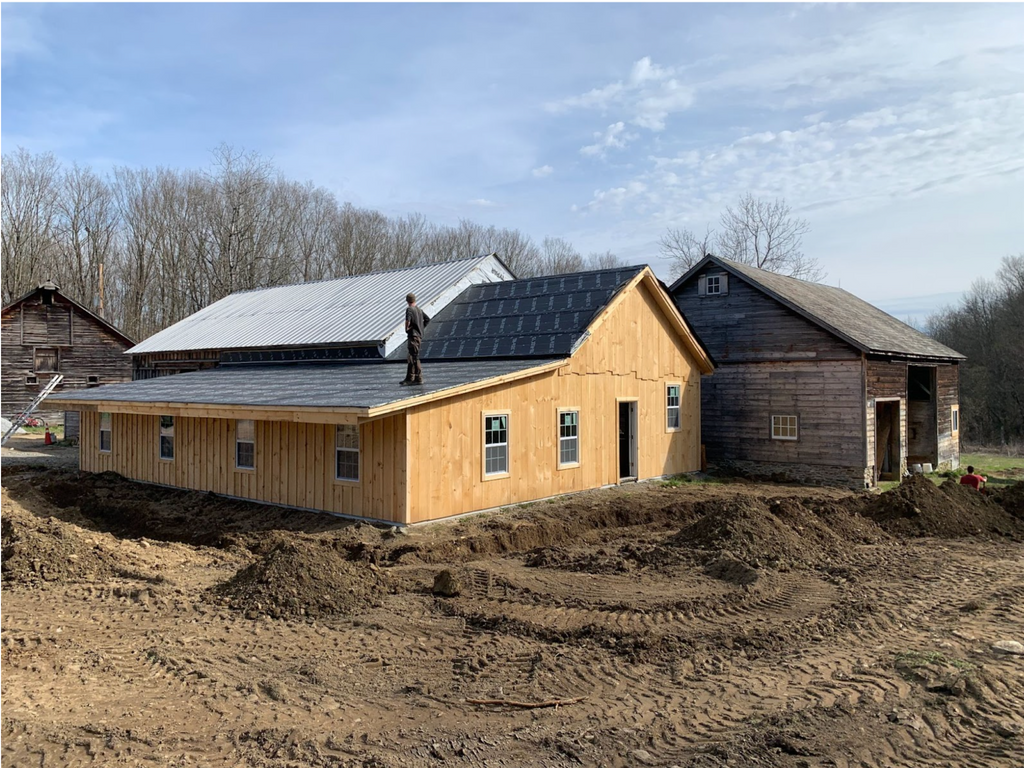
The New Wicks Forge Workshop: One Year Later
It's been 1 year since we moved into our new workshop and it's been non-stop construction and renovations ever since.
Just like the work we make, our workshop is a mix of old and new, eclectic and classic.
The original shop is an old dairy barn (our beloved finished pieces currently reside in the old milking parlor). Last year we started building 4 additions to the shop. One on each side of the original rectangle. Here's a look at our really complicated and professional original design:
While there is still a lot to do, we wanted to share the progress we've made so far–because we really have come a long way.
Every piece of steel we work moves through our shop from raw material to finished product. So let’s pretend you are a piece of steel and follow us on that journey through our space.
Metal Room
Metal usually comes in 20-foot lengths so we wanted a long and narrow room where we could both store it and cut it. While that seems simple enough, we have about 10 different types of saws, cutters, and shears depending on the size and type of material we're working with. The walls are a mixture of the original barn's old exterior wall, salvaged corrugated metal, and locally milled pine boards.
Forging Area
This is the main section of the original barn. Once steel is cut down, it's ready to be hot-forged into something cool. In order to preserve the old-school vibes, we've done as little as possible to this original space besides putting in floors and running electricity. This room is where the magic happens, and it's very fitting that the oldest part of our craft takes place in the oldest part of the building.
Welding Room
This space is where we do welding and fabrication once the pieces have been forged and shaped. We wanted a big open space for taking on any size project. We did a "gable" addition to mirror the original shape of the barn. The walls are salvaged corrugated metal roofing from another (even older) barn.
Loud Room
Once the pieces have been made, they need to be cleaned so they can eventually have a nice finished surface. While many of our tools are loud, a few are horrendously so. We put them all together and built a special room for them that's padded with noise-deadening insulation so they can be as loud as they want. Most of the machines in there are types of homemade "tumblers" that spin around and clean the metal after it's been forged. As if blacksmithing wasn't dirty enough, this process creates oodles of dirty metal flakes. So naturally, we painted the room the same color as these metal flakes to help hide the grime.
Finishing Area
Once the metal is cleaned, it goes into our modified commercial pizza oven to get heated up again and then dipped in our finishing solution. Three of the shop’s additions were "stick-framed," which means 2x6 walls and modern building methods. This 4th edition is our covered outdoor finishing area and was “timber-framed”, basically old-school post and beam style. We salvaged existing timber posts and beams from the property, as well as a few trees we sawed ourselves on-site.
Milk Room
Once the pieces are finished, they get sorted and eventually shipped out. This is where they live until they get packaged and sent off to begin their next adventure with our customers.
The first thing we did was pour concrete floors in the shop. Because of this, or because people were shorter 100 years ago, the ceilings on this room were only 5' 6". Fine for cows, not ideal for humans.
The walls and ceiling were also covered in this ancient limewash paint that was chipped and peeling everywhere. We jacked up the ceiling (not sketchy at all, we promise), did tons of sanding, got lime dust over every surface on the entire farm, built storage shelves all over, and honored that horrendous-to-remove original paint job by doing a modern whitewash on the walls.
Chill Zone
Directly above the milking parlor is (what will eventually be) our lounge. The floors were rotted and covered in 50 years of accumulated bat poop. We used the guano to fertilize the lawn, put new floors in, insulated the walls and utilized leftover construction materials to do the new interior walls. We're still waiting to find a giant window on Craigslist for that center space.
Next Chapter
While it's been non-stop work to get the place up and running, it's worth it because we are lucky enough to love what we do. This is a crazy space (the goblin workshop lives on), but it's also a dream come true for all of us who get to work in it. And it is only possible because of the support of our amazing customer base. Thanks for taking a walk-through with us and an even bigger thank you for helping the workshop come alive.
Leave a comment